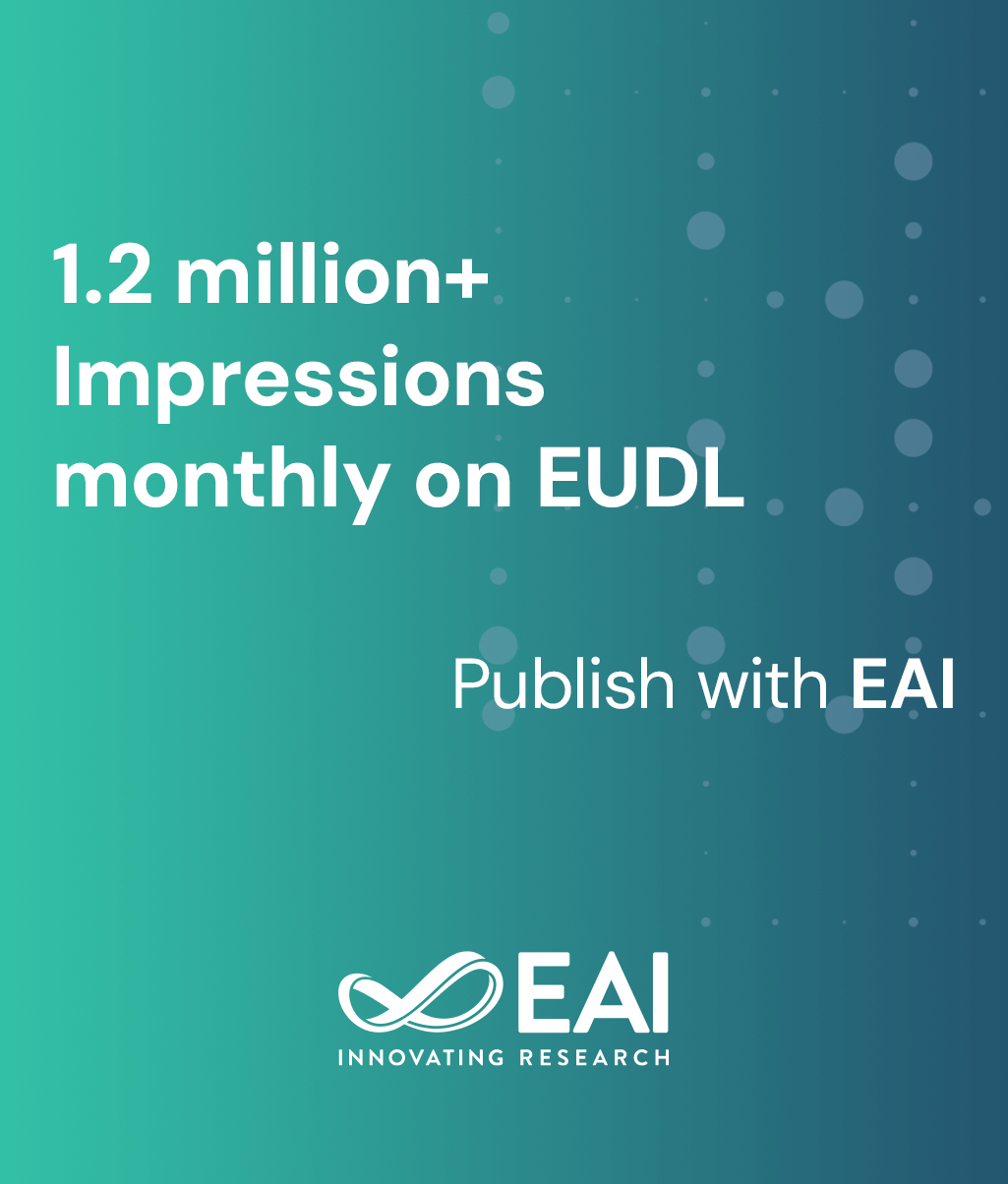
Research Article
PLC Based PID for Wrapping Machine Tension Control
@INPROCEEDINGS{10.4108/eai.20-1-2018.2281878, author={Sujono Sujono and Muhtadin Muhtadin}, title={PLC Based PID for Wrapping Machine Tension Control}, proceedings={Proceedings of the 1st Workshop on Multidisciplinary and Its Applications Part 1, WMA-01 2018, 19-20 January 2018, Aceh, Indonesia}, publisher={EAI}, proceedings_a={WMA-1}, year={2019}, month={9}, keywords={control system pid tension plc wrapping}, doi={10.4108/eai.20-1-2018.2281878} }
- Sujono Sujono
Muhtadin Muhtadin
Year: 2019
PLC Based PID for Wrapping Machine Tension Control
WMA-1
EAI
DOI: 10.4108/eai.20-1-2018.2281878
Abstract
The process of wrapping with plastics to better ensure the safety of the goods are mostly done, such as goods before being put into the trunk of the plane or when the industrial product to be delivered in long distances. In the wrapping process, the tension of the tension of the plastic (wrapping material) is very important to keep its value so that it will produce a wrapping that is in accordance with the desired. In this paper will be presented about the implementation of PID (Proportional Integral Differential) controller for tension control on wrapping machine. The system consists of a three phase induction motor as a drive in the unwinder and rewinders, PIDs of the PLC, inductive proximity as a plastic tension sensor, and a PC for data entry and system monitoring. The tension control of the plastic wrapping material is carried out by manipulating the unwinder velocity for the rewinder speed which is maintained at a constant speed. The speed difference between the two motors (unwinder and rewinder) will produce tension. To get good control performance, PID parameter tuning is required. From tuning using 3 methods (reaction curve method, tuning PID TIA PORTAL tool and Dotx PID tuner application), the best result resulted with 3.3% overshoot response, 1.7 second rise time, 3.2% settling time second, there is 1 oscillation and steady state error of 0.263%.