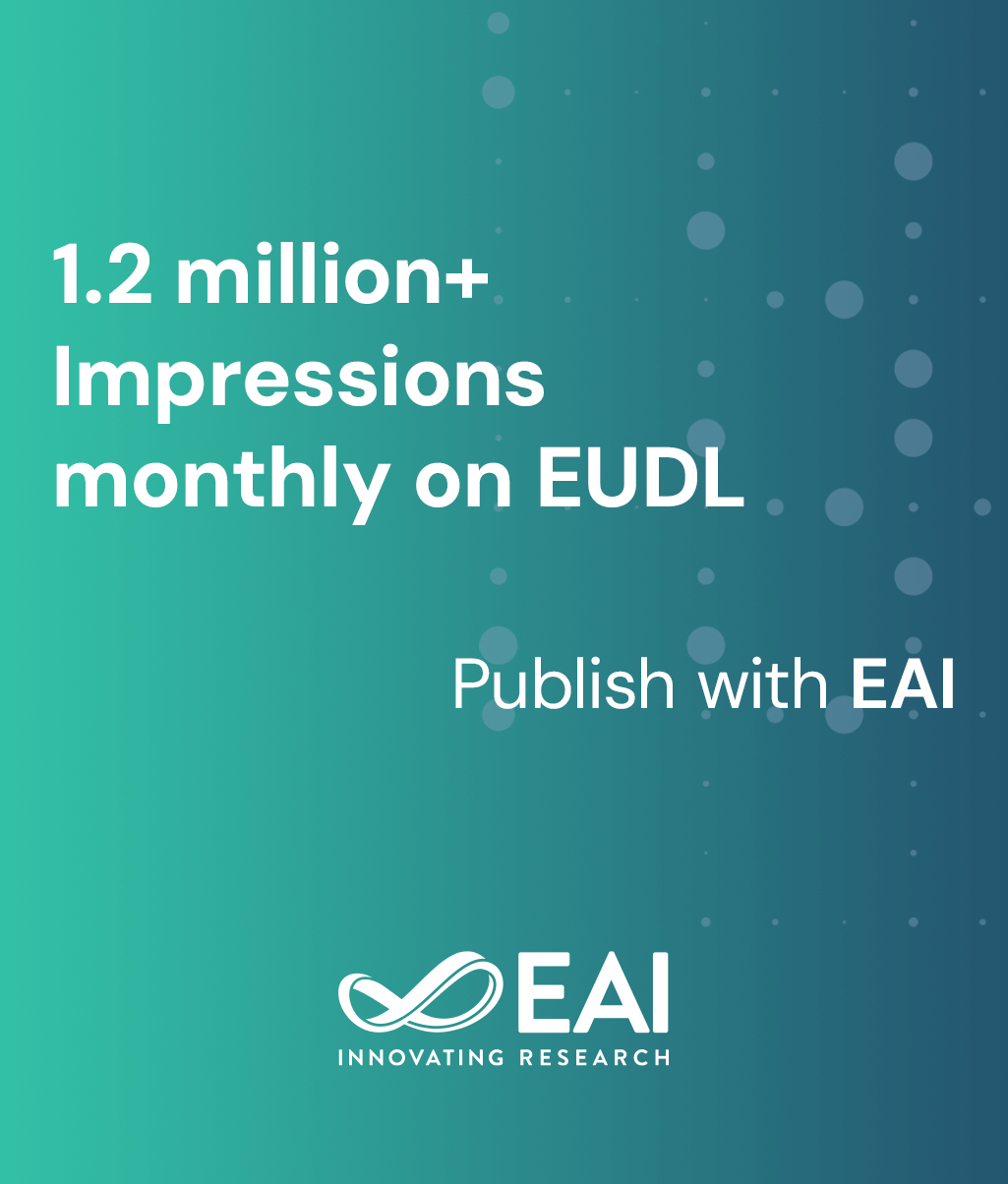
Research Article
Design and Simulation of Waste Heat Recovery System for Heavy Oil Preheating in Dashen Brewery Company
@INPROCEEDINGS{10.1007/978-3-030-43690-2_43, author={Addisu Kebede and Abdulkadir Hassen}, title={Design and Simulation of Waste Heat Recovery System for Heavy Oil Preheating in Dashen Brewery Company}, proceedings={Advances of Science and Technology. 7th EAI International Conference, ICAST 2019, Bahir Dar, Ethiopia, August 2--4, 2019, Proceedings}, proceedings_a={ICAST}, year={2020}, month={6}, keywords={Waste heat recovery Head loss Shell and tube heat exchange}, doi={10.1007/978-3-030-43690-2_43} }
- Addisu Kebede
Abdulkadir Hassen
Year: 2020
Design and Simulation of Waste Heat Recovery System for Heavy Oil Preheating in Dashen Brewery Company
ICAST
Springer
DOI: 10.1007/978-3-030-43690-2_43
Abstract
Industrial waste heat refers to energy that is generated in industrial processes without being put to practical use. In this paper an effort has made about waste heat recovery system design for Dashen Brewery Company. It is tried to identify source of waste heat and design a new plant layout for the purpose of waste heat recovery. In Dashen brewery company heat is basically lost at the boiler, process water heater pipe and Wort kettle chimney. The company uses heavy oil for boiler and this oil needs to be heated to convert in to light oil for better ignition. To heat this heavy oil the company still uses steam but this paper design a system to use exhaust steam at Wort kettle for heating of heavy oil instead of steam. Tasks performed in in this paper are direct temperature measurement on the waste heat source, heat loss calculation on the chimney and construct appropriate waste heat recovery routine. Head loss and other basic flow parameters had been considered. Furthermore from the analytical model it is possible to determine the amount of power needed to the boiler which is 56.947 MW from 6220 L/h of furnace oil and from exhaust steam 17.5 kW is gained which can burn 190 L/h of fuel; in terms of birr it is possible to save 456 L/day × 19.5 birr which is 8892 birr per day.