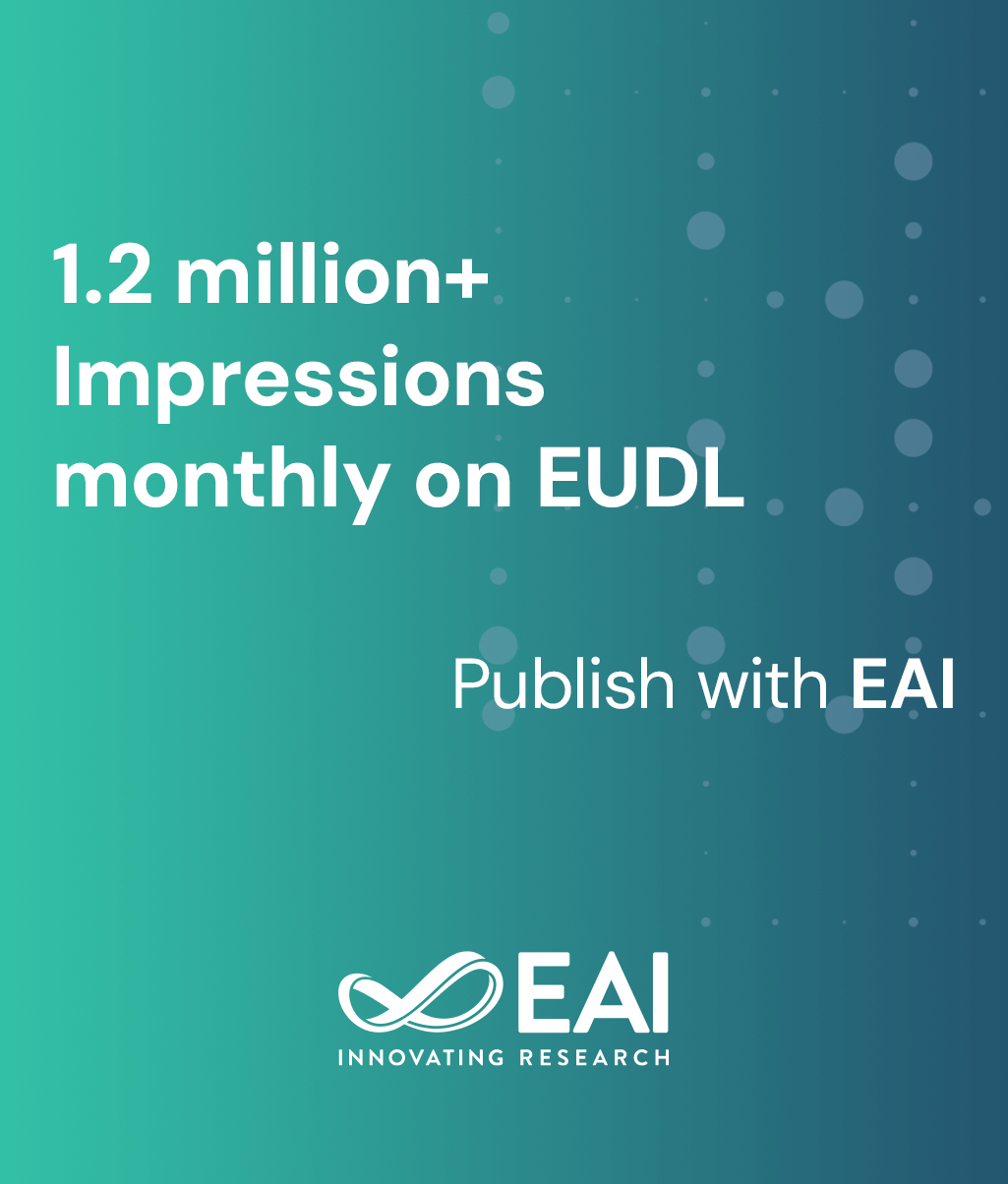
Research Article
Topology Optimization of an Inter-Island Aircraft Rudder Quadrant Using Finite Element Method
@INPROCEEDINGS{10.4108/eai.8-11-2023.2345845, author={Rizky Akmal Putera and Budi Aji Warsiyanto and Josua Sitinjak and Fajar Ari Wandono}, title={Topology Optimization of an Inter-Island Aircraft Rudder Quadrant Using Finite Element Method}, proceedings={Proceedings of the 2nd International Conference on Aviation Industry, Education, and Regulation, AVINER 2023, 8-9 November 2023, Jakarta, Indonesia}, publisher={EAI}, proceedings_a={AVINER}, year={2024}, month={5}, keywords={topology optimization quadrant structure finite element method mass reduction}, doi={10.4108/eai.8-11-2023.2345845} }
- Rizky Akmal Putera
Budi Aji Warsiyanto
Josua Sitinjak
Fajar Ari Wandono
Year: 2024
Topology Optimization of an Inter-Island Aircraft Rudder Quadrant Using Finite Element Method
AVINER
EAI
DOI: 10.4108/eai.8-11-2023.2345845
Abstract
Topology optimization has become an effective tool for mass reduction and good performance, especially in aeronautics and aerospace engineering. This research applies topology optimization using the finite element method (FEM) on the aircraft rudder quadrant structure of a 19 passengers inter-island aircraft. The analysis was performed by considering the maximum stress, mass reduction, and displacement that occur on the aircraft rudder quadrant in the initial and final design. In the initial design with a mass of 544.5 grams, the maximum stress and maximum displacement that occur is 24.4 MPa and 0.473 mm, respectively. In the final design, the mass reduction obtained is 13.77%, namely 469.5 grams, with a maximum stress of 22.6 MPa and maximum displacement of 0.579 mm. The static test results obtained after the redesign have decreased the maximum stress. This is because fillets can reduce the angular roughness between two surfaces, thereby increasing a more even stress distribution. It is expected that the implementation of the topology optimization on the quadrant component could comply with the required strength.