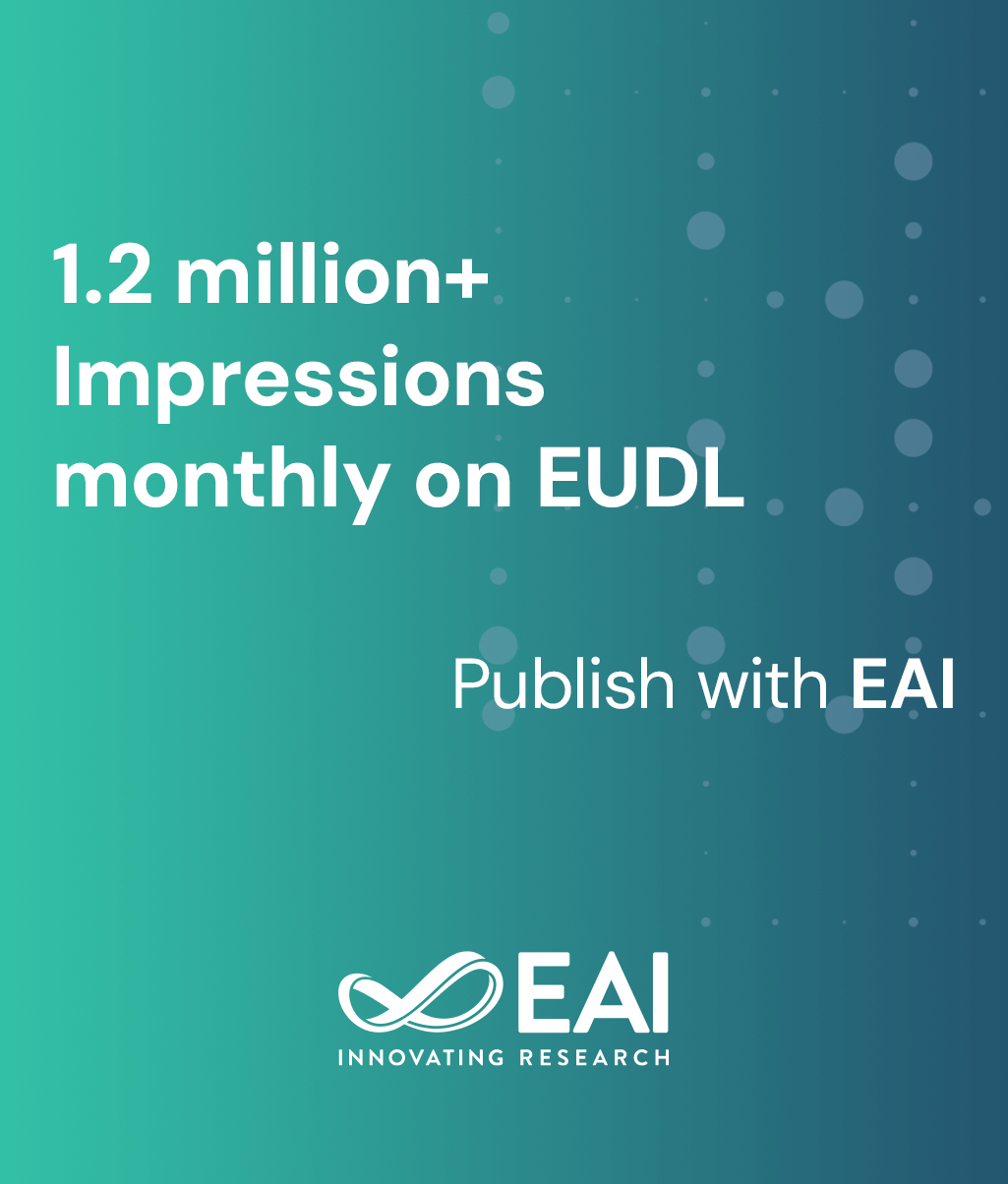
Research Article
Simulation of Stress Distribution on Slotted Flap Mechanism Using Finite Element Method
@INPROCEEDINGS{10.4108/eai.8-11-2023.2345838, author={Juan Harris Yedidja Malega and Agus Suprianto and Muhammad Hadi Widanto}, title={Simulation of Stress Distribution on Slotted Flap Mechanism Using Finite Element Method }, proceedings={Proceedings of the 2nd International Conference on Aviation Industry, Education, and Regulation, AVINER 2023, 8-9 November 2023, Jakarta, Indonesia}, publisher={EAI}, proceedings_a={AVINER}, year={2024}, month={5}, keywords={stress distribution finite element aerodynamic characteristic slotted flap}, doi={10.4108/eai.8-11-2023.2345838} }
- Juan Harris Yedidja Malega
Agus Suprianto
Muhammad Hadi Widanto
Year: 2024
Simulation of Stress Distribution on Slotted Flap Mechanism Using Finite Element Method
AVINER
EAI
DOI: 10.4108/eai.8-11-2023.2345838
Abstract
Slotted flaps are one of the most common types of flaps used in aerospace engi-neering providing significant benefits to aircraft performance during flight phases, by increasing wing area and improving lift force during takeoff and landing. This research paper describes a methodical approach to studying the aerodynamic and structural behavior of a slotted flap mechanism using computer simulations. The process begins with a thorough review of existing literature and the development of a Computer-Aided Design (CAD). Simulations are then conducted using ad-vanced software that combines Computational Fluid Dynamics (CFD) and Finite Element Analysis (FEA). The results from the simulations are seamlessly import-ed from CAD platform for further analysis. The paper explores four variations of the flight phase. Each with different configurations and velocities and examines their effects on lift distribution and stress tension. The integration of the flap de-sign into the simulation platform allows for precise analysis, including material analysis and load location insights. The central finding of the variations reveals maximum stress results ranging from 135 to 435 Megapascals (MPA), providing valuable insights for optimizing the design in both aerodynamic and structural as-pects.