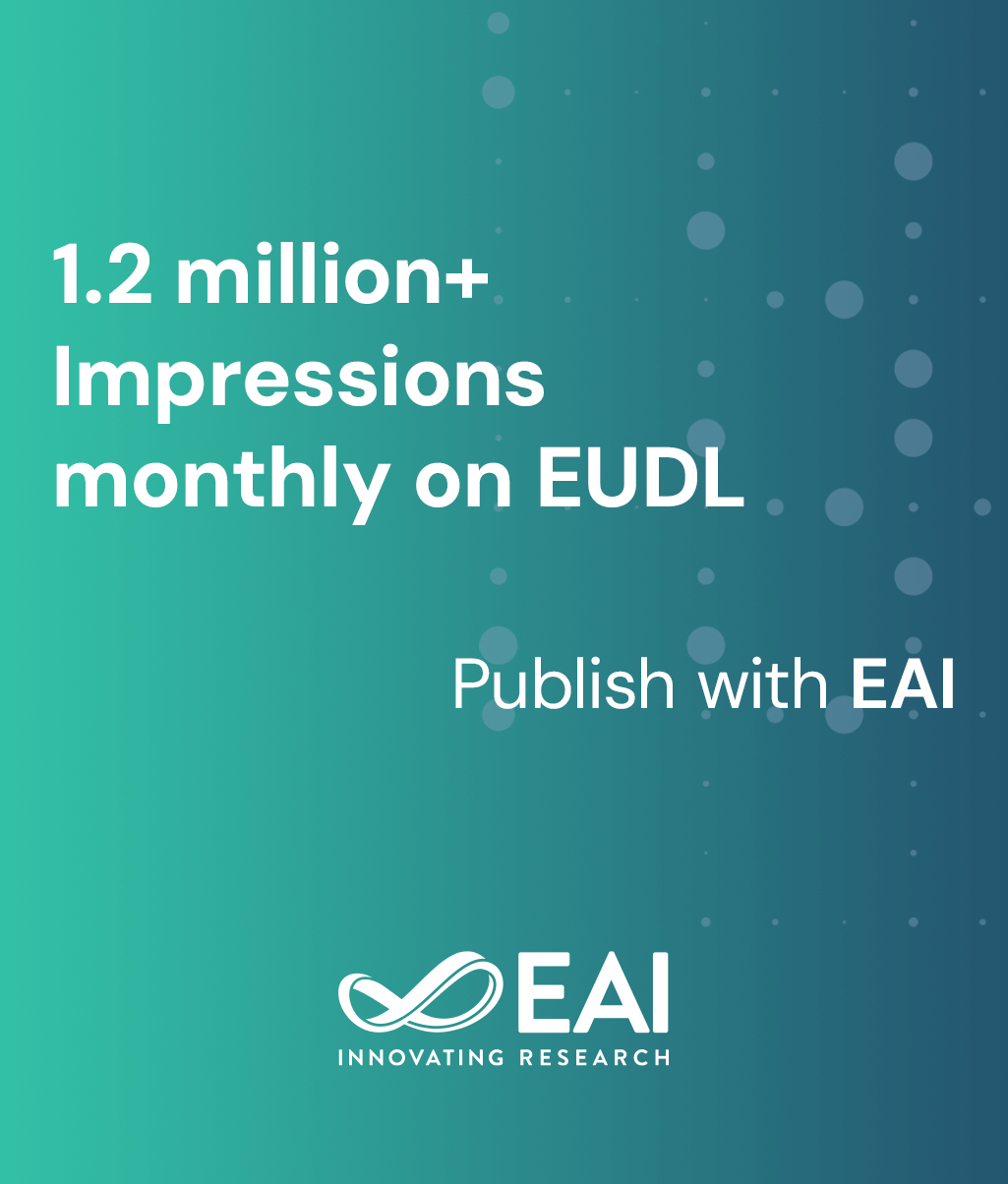
Research Article
System Design Warehouse Management AGV for Packages Sorting in Supporting Industry E-Commerce
@INPROCEEDINGS{10.4108/eai.5-10-2022.2329535, author={Mohamad Nasyir Tamara and Abdurahman Dwijotomo and Novian Fajar Satria and Endra Pitowarno and Didik Setyo Purnomo and Cahyo Sugianto and Wildan Hilmy}, title={ System Design Warehouse Management AGV for Packages Sorting in Supporting Industry E-Commerce}, proceedings={Proceedings of the 5th International Conference on Applied Engineering, ICAE 2022, 5 October 2022, Batam, Indonesia}, publisher={EAI}, proceedings_a={ICAE}, year={2023}, month={6}, keywords={agv ddmr e-commerce industry pid control}, doi={10.4108/eai.5-10-2022.2329535} }
- Mohamad Nasyir Tamara
Abdurahman Dwijotomo
Novian Fajar Satria
Endra Pitowarno
Didik Setyo Purnomo
Cahyo Sugianto
Wildan Hilmy
Year: 2023
System Design Warehouse Management AGV for Packages Sorting in Supporting Industry E-Commerce
ICAE
EAI
DOI: 10.4108/eai.5-10-2022.2329535
Abstract
The e-commerce industry has used a lot of goods sorting technology using AGV (Automated Guided Vehicle). Goods, moved automatically using an autonomous system can increase the effectiveness and efficiency of the process. The benefits of Sorting AGV are felt when a large number of goods (thousands to millions) must be delivered within a single day. For that we need an adequate autonomous AGV system that has the features to handle the job. This research focuses on mechanical design with mechanization that can support the entire system and the application of AGV motion control in order to run well from varying packet loads to be delivered. For fast movement and ease of control, the Differential Drive Mobile Robot (DDMR) model is chosen which is equipped with a flipping mechanism to drop the packet. The controller based on PID control is applied for first functional movement experiment to review the robot performance from transported various loads. From the preliminary experiment the robot is able to lift the load up to 42 kg and no significant different of position and velocity responds.