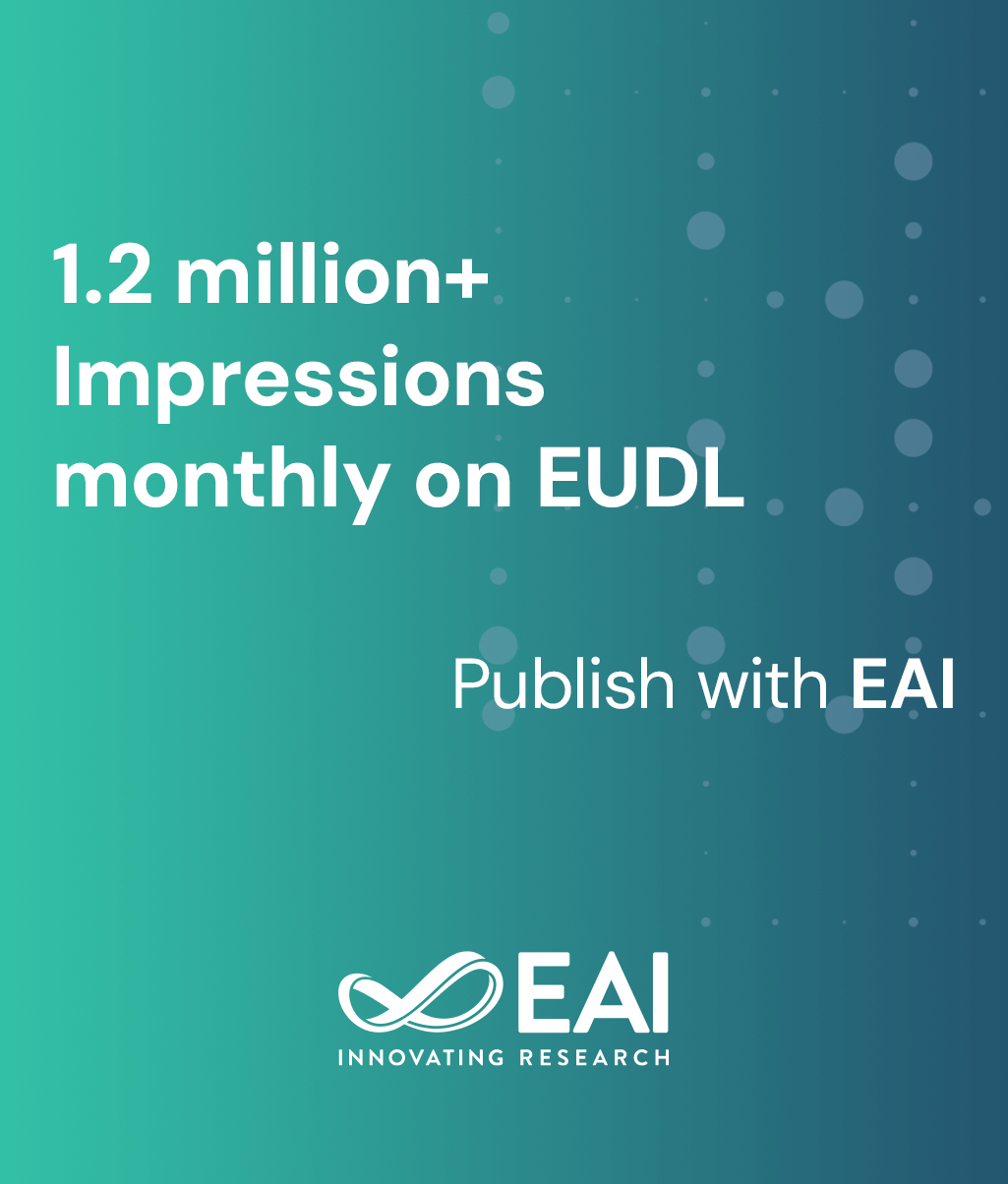
Research Article
Occupational Risk Assessment Using the Failure Mode and Effect Analysis (FMEA) Method in the Production Room of Bearing Industry
@INPROCEEDINGS{10.4108/eai.31-3-2022.2320941, author={Yusri Handoko and Ari Rahman and Fatimah D Qonitan and Sustina Bayu}, title={Occupational Risk Assessment Using the Failure Mode and Effect Analysis (FMEA) Method in the Production Room of Bearing Industry }, proceedings={Proceedings of the 1st International Conference on Contemporary Risk Studies, ICONIC-RS 2022, 31 March-1 April 2022, South Jakarta, DKI Jakarta, Indonesia}, publisher={EAI}, proceedings_a={ICONIC-RS}, year={2022}, month={8}, keywords={bearing failure mode effect analysis (fmea) production area risk assessment risk priority number (rpn)}, doi={10.4108/eai.31-3-2022.2320941} }
- Yusri Handoko
Ari Rahman
Fatimah D Qonitan
Sustina Bayu
Year: 2022
Occupational Risk Assessment Using the Failure Mode and Effect Analysis (FMEA) Method in the Production Room of Bearing Industry
ICONIC-RS
EAI
DOI: 10.4108/eai.31-3-2022.2320941
Abstract
PT X is an industry engaged in the manufacturing of bearings. This study aims to conduct an occupational risk assessment in the production room of PT X using failure mode and effect analysis (FMEA). The results of risk assessment in 5 working areas in the Production Room resulted in the risk priority number (RPN) value of the raw material storage area were 687, combustion area (30), assembly area (1481), packaging area (296), and the delivery area (432). RPN calculation on FMEA showed that the assembly area has the most significant RPN value, so it was prioritized for risk control measures. The controlling efforts were providing sticks and machine protective covers, replacing damaged button covers, machine operator training, improving standard operating procedures (SOP), and others. Therefore, controlling the risk was expected to reduce the potential risk of a work accident.