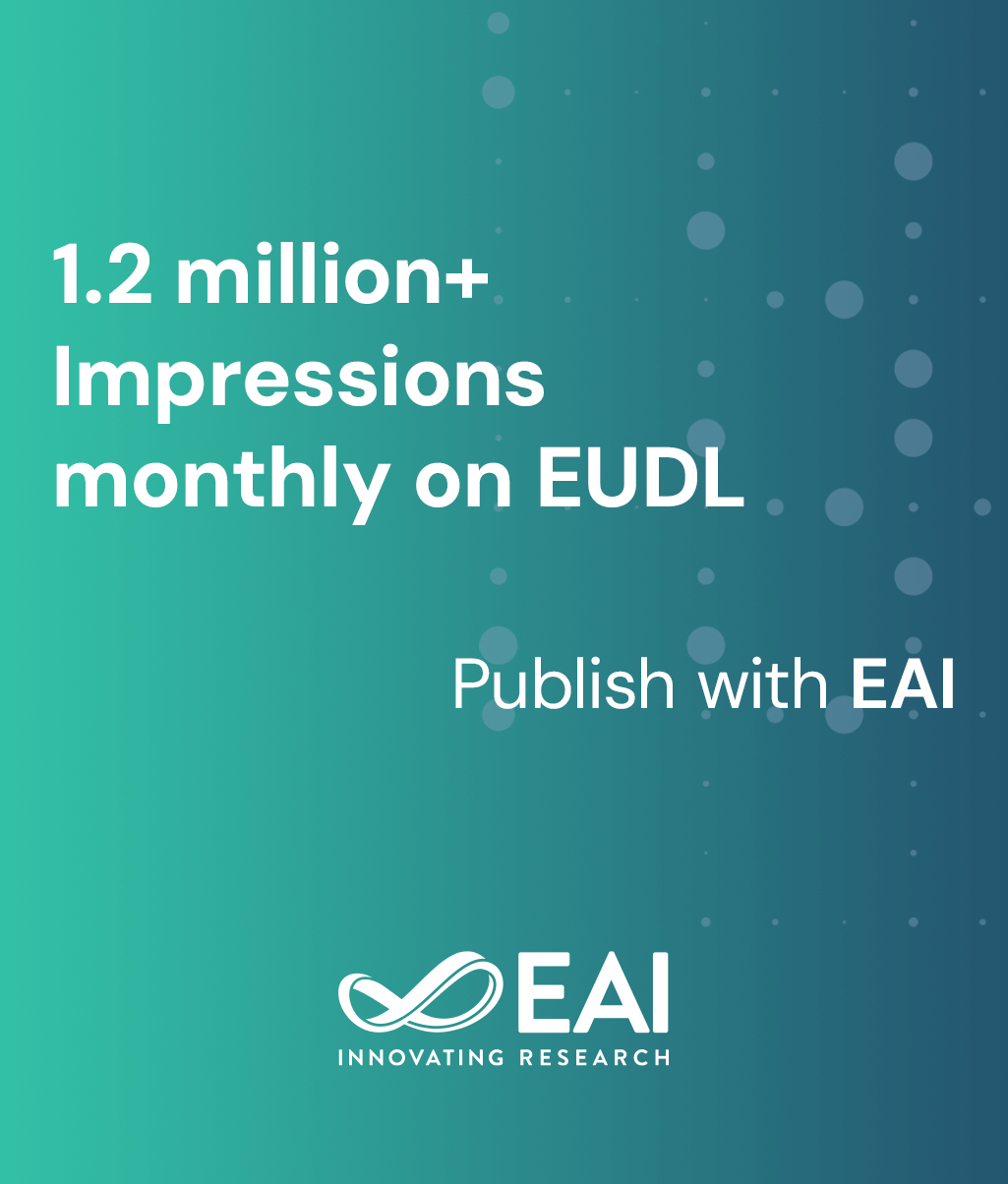
Research Article
Simulation and Prototyping of a Two-Phase Inverter to Drive an Asymmetrical Single-Phase Induction Motor
@INPROCEEDINGS{10.4108/eai.27-11-2021.2315635, author={I Putu Suka Arsa and I Wayan Sutaya and I Gede Nurhayata and I Gede Ratnaya and I Gede Siden Sudaryana}, title={Simulation and Prototyping of a Two-Phase Inverter to Drive an Asymmetrical Single-Phase Induction Motor}, proceedings={Proceedings of the 4th International Conference on Vocational Education and Technology, IConVET 2021, 27 November 2021, Singaraja, Bali, Indonesia}, publisher={EAI}, proceedings_a={ICONVET}, year={2022}, month={2}, keywords={single-phase motor two-phase inverter spwm}, doi={10.4108/eai.27-11-2021.2315635} }
- I Putu Suka Arsa
I Wayan Sutaya
I Gede Nurhayata
I Gede Ratnaya
I Gede Siden Sudaryana
Year: 2022
Simulation and Prototyping of a Two-Phase Inverter to Drive an Asymmetrical Single-Phase Induction Motor
ICONVET
EAI
DOI: 10.4108/eai.27-11-2021.2315635
Abstract
Nowadays, a single-phase induction motor can be found in almost all electronic devices, especially for applications that use low power. This motor has one speed. A certain application requires this motor to have a speed variable generally uses mechanical techniques such as gears or sometimes electrical grouping windings. However, true variable speed will not be obtained, consuming more energy. The most precise way to control the speed of this motor is to use an inverter where the output voltage and frequency are variable. As it is known that a single-phase of the induction motor is a motor consisting of two windings. Alternating current flowing into each winding must have a phase difference of 900. This paper discusses the research of a two-phase inverter with a simulation in MATLAB and prototyping. The driver circuit of the inverter used the three-legged method. Two legs were used as alternating voltage outputs, with a phase difference of 900. One leg was used as common. Each leg consisted of a pair of IGBT with input in the form of SPWM voltage generated from signal modulation. From the inverter prototype that has been made, the inverter has driven the motor to rotate. Many harmonic signals in the current flowing to the motor were still found due to non-ideal component factors. Further research will be better to reduce the harmonic signals in the current windings to produce better rotation.