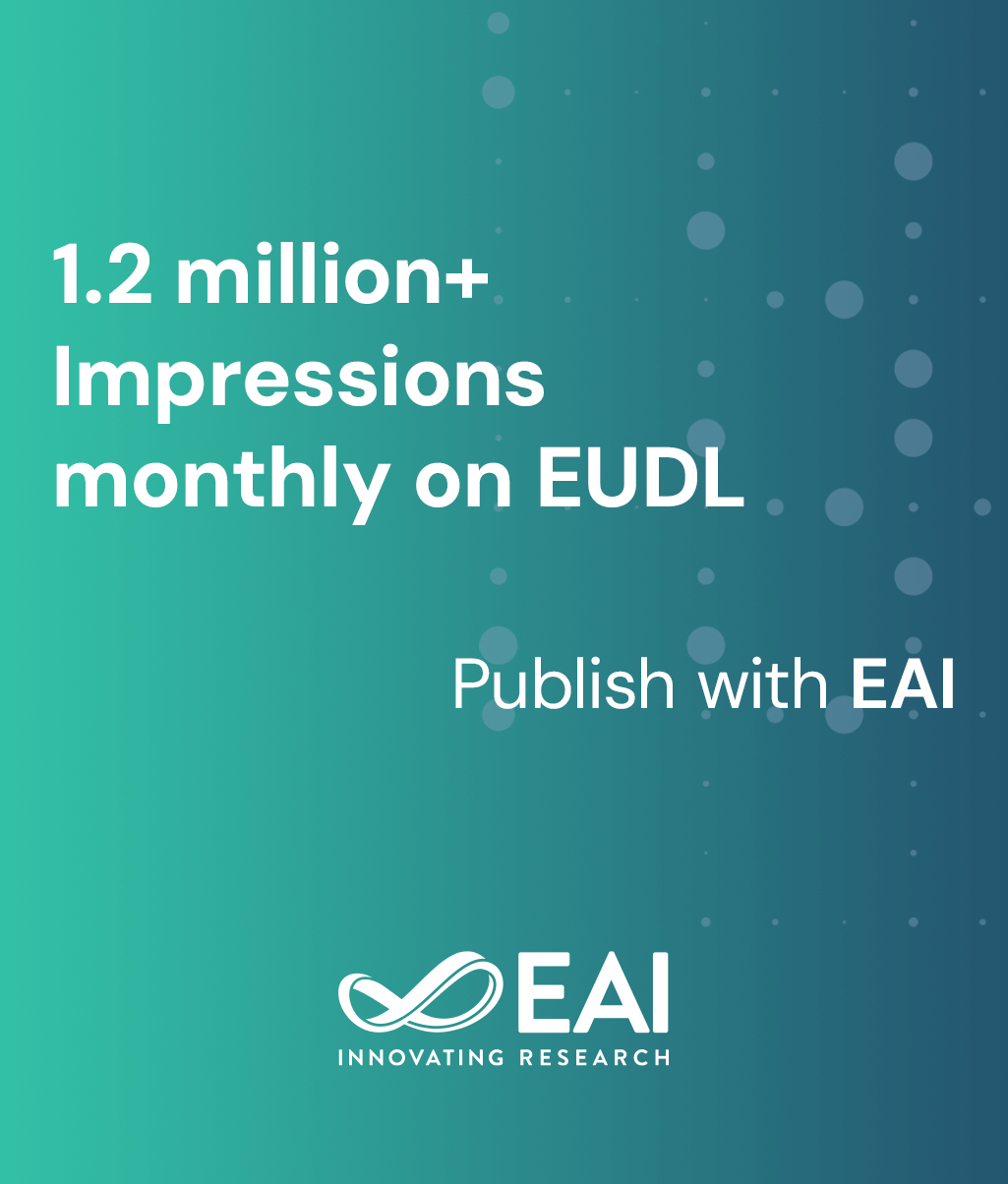
Research Article
The Conversion Cycle: Review of Material Requirements Planning (MRP)
@INPROCEEDINGS{10.4108/eai.25-11-2021.2318831, author={Juninetenth Keeply F Sitanggang and Iskandar Muda}, title={The Conversion Cycle: Review of Material Requirements Planning (MRP)}, proceedings={Proceedings of the 1st International Conference on Social, Science, and Technology, ICSST 2021, 25 November 2021, Tangerang, Indonesia}, publisher={EAI}, proceedings_a={ICSST}, year={2022}, month={7}, keywords={conversion cycle; material requirements planning}, doi={10.4108/eai.25-11-2021.2318831} }
- Juninetenth Keeply F Sitanggang
Iskandar Muda
Year: 2022
The Conversion Cycle: Review of Material Requirements Planning (MRP)
ICSST
EAI
DOI: 10.4108/eai.25-11-2021.2318831
Abstract
The purpose of this paper is to determine the planning of raw material requirements using MRP (Material Requirements Planning). The analysis method uses descriptive analysis by performing the MRP stages which are carried out, among others: Making Bill of Materials, Making product structures, Forecasting: quadratic method, cyclical method, linear regression, MPS (Master Planning Schedule), Creating production schemes, Creating Product Structures, Planning Raw Materials, Master production scheduling, Calculation of raw material requirements using the Lot For Lot (LFL) method, Least Unit Cost (LUC) method. Secondary data taken in the company is data on sales and raw materials. Planning for raw materials requires forecasting the next month's sales using the cyclical method. The results of the calculation of raw material planning obtained a monthly production forecast of 7 units of product with an average order time of 3 months. With MRP, companies can better control inventory and delivery times of raw materials, ensuring that materials can arrive at roughly the exact time they are needed in the production process. In addition, by using the MRP method inventory costs are reduced, because with the MRP method a company can control inventory so that there is no excess inventory and delays in delivery of goods.