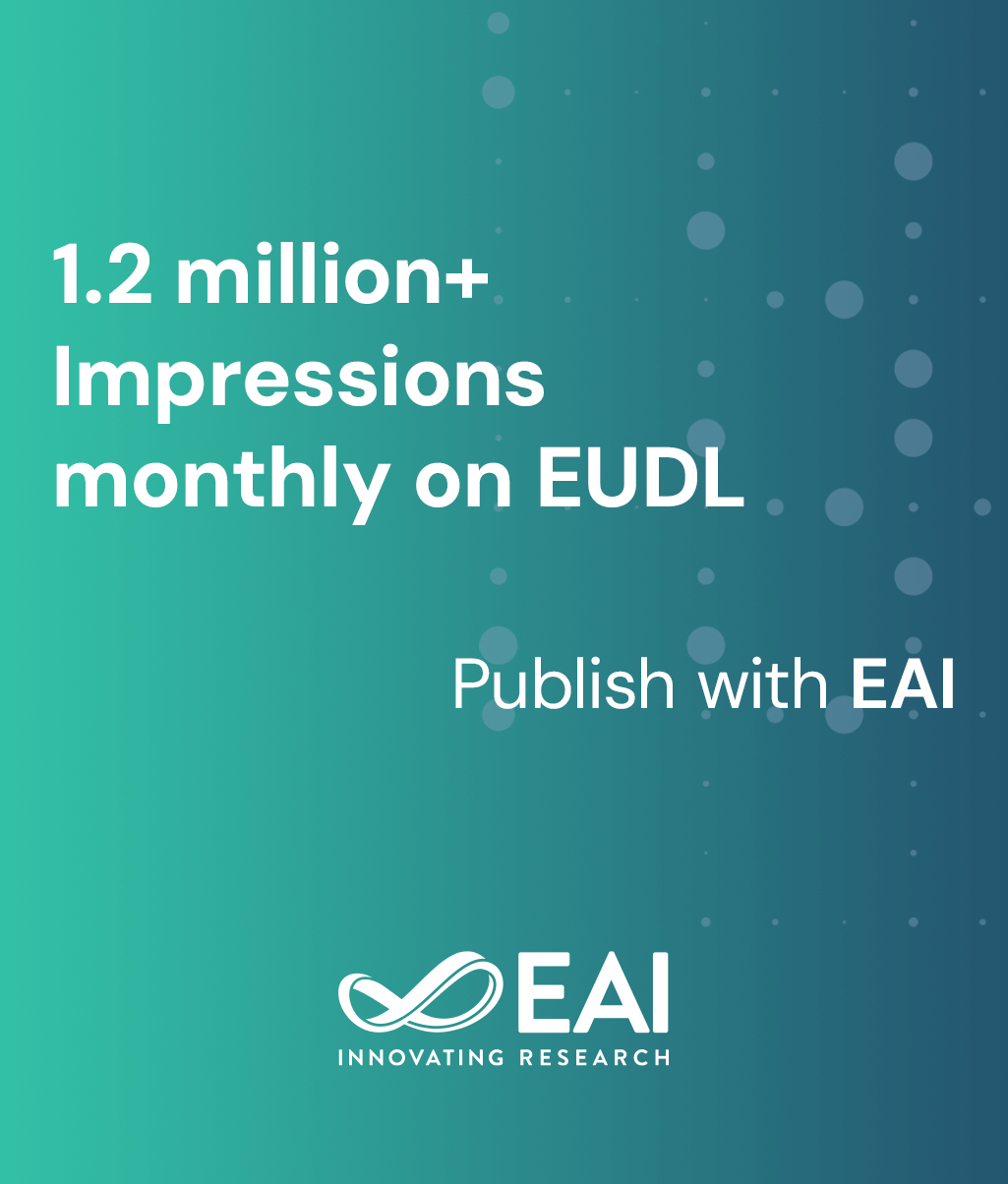
Research Article
Implementation of Value Stream Mapping in Pump Industry
@INPROCEEDINGS{10.4108/eai.23-2-2024.2347033, author={Maharasi P B and Jenina Pushpam G and Vigneswaran C and Brajesh Kumar Kanchan and Madhan Mohan G}, title={Implementation of Value Stream Mapping in Pump Industry}, proceedings={Proceedings of the International Conference on Advancements in Materials, Design and Manufacturing for Sustainable Development, ICAMDMS 2024, 23-24 February 2024, Coimbatore, Tamil Nadu, India}, publisher={EAI}, proceedings_a={ICAMDMS}, year={2024}, month={6}, keywords={lean manufacturing value stream mapping kaizen}, doi={10.4108/eai.23-2-2024.2347033} }
- Maharasi P B
Jenina Pushpam G
Vigneswaran C
Brajesh Kumar Kanchan
Madhan Mohan G
Year: 2024
Implementation of Value Stream Mapping in Pump Industry
ICAMDMS
EAI
DOI: 10.4108/eai.23-2-2024.2347033
Abstract
The pump industry provides the machinery and systems necessary for fluid movement, making it a cornerstone of modern society and industry. Without pumps, many essential processes across various sectors would be inefficient, if not impossible, to carry out. In order to increase performance across the entire pump industry, the cycle time has been reduced. Lean manufacturing, which has its roots in Japan and was developed there, is regarded as a business strategy to eliminate waste, improving productivity by producing goods of higher quality and accuracy, particularly for small and medium-sized businesses (SMEs). Among all other lean practises, value stream mapping (VSM) and kaizen principles are the most effective in practice. Additionally, similar lean technologies are used in pump assembly in medium-sized businesses to find and eliminate waste in this case study. The current value stream mapping (CVSM) used in this instance is used to initially visualize the process route. After monitoring the entire process, wastes that have an impact on the cycle time are then discovered and analysed. The Kaizen principle is then applied to minimize waste in the process, and a future value stream mapping (FVSM) is created to examine the root causes of waste generation. The considering pump industry will undoubtedly be able to increase productivity, competitiveness, and cycle time with the help of this capabilities.