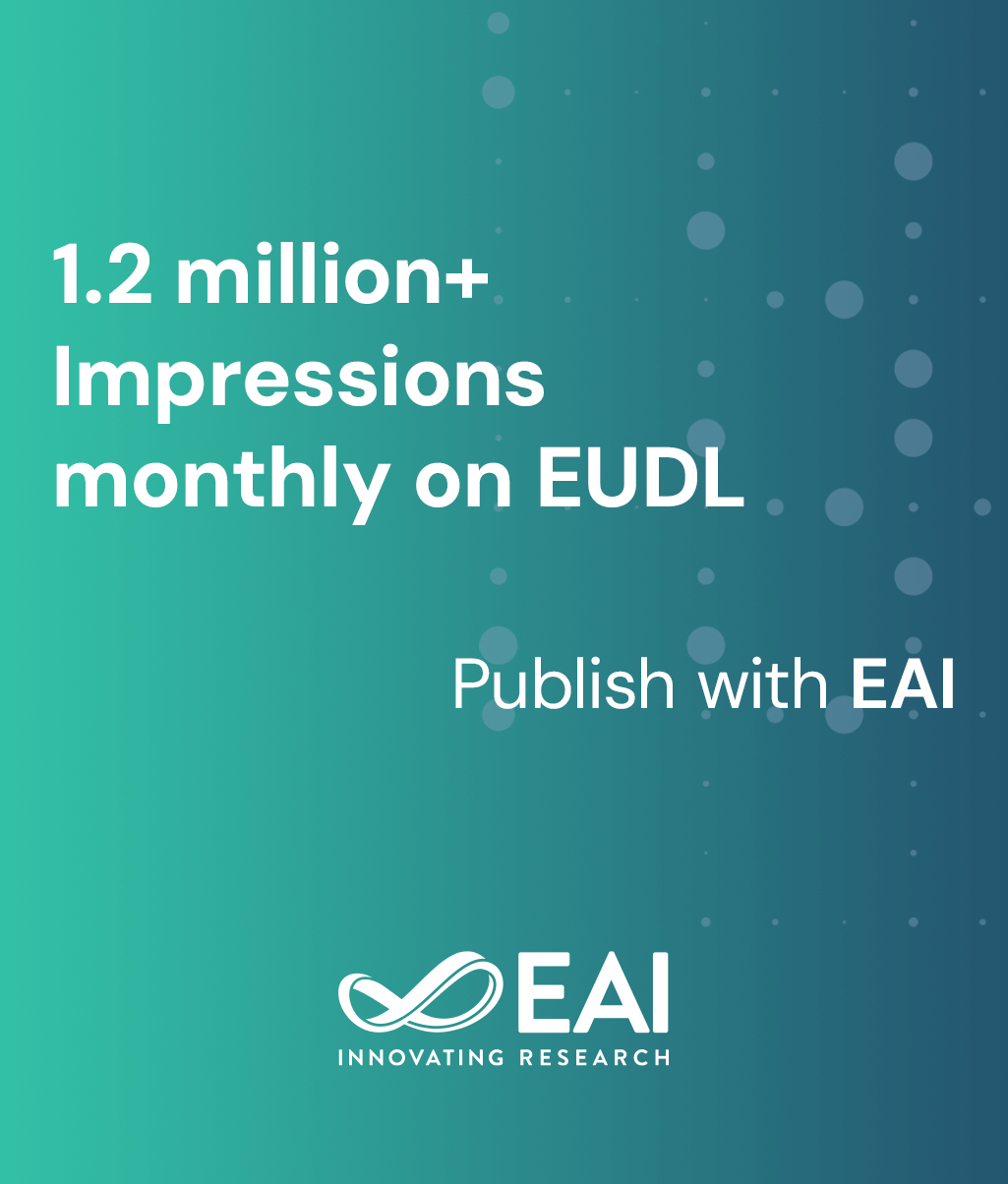
Research Article
Defect Identification in Weld Beads of Aluminium 5356 Using Liquid Penetrant Test
@INPROCEEDINGS{10.4108/eai.23-2-2024.2347024, author={Saravanakumar K and Medoline J and Ananth S and Sansuuki Priyanka K M and Dharshini M}, title={Defect Identification in Weld Beads of Aluminium 5356 Using Liquid Penetrant Test}, proceedings={Proceedings of the International Conference on Advancements in Materials, Design and Manufacturing for Sustainable Development, ICAMDMS 2024, 23-24 February 2024, Coimbatore, Tamil Nadu, India}, publisher={EAI}, proceedings_a={ICAMDMS}, year={2024}, month={6}, keywords={gas metal arc welding aluminium 5356 alloy l9 orthogonal array liquid penetrant test}, doi={10.4108/eai.23-2-2024.2347024} }
- Saravanakumar K
Medoline J
Ananth S
Sansuuki Priyanka K M
Dharshini M
Year: 2024
Defect Identification in Weld Beads of Aluminium 5356 Using Liquid Penetrant Test
ICAMDMS
EAI
DOI: 10.4108/eai.23-2-2024.2347024
Abstract
In this paper work, gas metal arc welding process was used to form weld bead. Aluminium (Al) 6082 acts as base plate and the Aluminium 5356 alloy acts as filler material. Argon (99.99%) is used as inert gas. The process parameters used in this research work were current (Ampere), stick-out distance (mm), and travel speed (mm/s). Nine beads were welded using an L9 orthogonal array. The optimal parameter was identified by using the Liquid Penetrant Test (LPT) method and also weld defects were identified. The zig-zag tool path strategy is used as it reduces thermal distortion and residual stress caused during welding which can be used for future research work. The first three samples and last two samples show the weld defect like undercut. The remaining beads exhibited with excess weld bead. The sixth bead has no defect. The process parameters value like current (120 Amp), stick-out distance (12 mm) and travel speed (3 mm/s) were chosen based on LPT and weld bead quality. Thus, it was chosen as the ideal bead in this current study. These parameter values can be used to produce multiwall-layered structure using WAAM, for Al 5356 alloy. A multiwall-layered structure can be built using WAAM (wire arc additive manufacturing) technique as it has acquired more recognition because of its increase in efficiency and ability to weld big components in a lesser time.