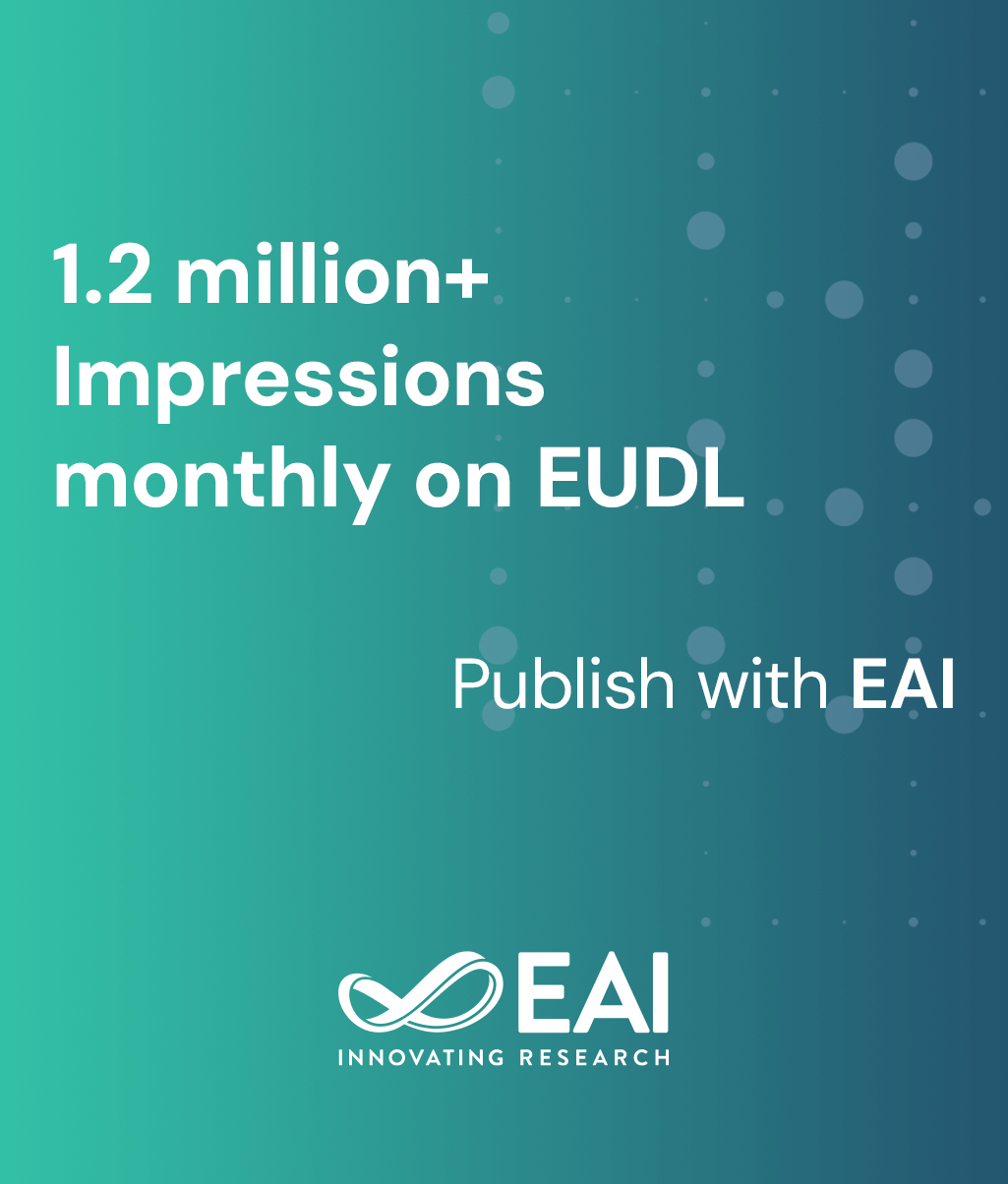
Research Article
A Framework of Nanomechanical Communication Systems Based on State Transitions
@INPROCEEDINGS{10.4108/eai.22-3-2017.152410, author={Ahmed Nasif and Mohammad Upal Mahfuz and Jagadeep Thota}, title={A Framework of Nanomechanical Communication Systems Based on State Transitions}, proceedings={10th EAI International Conference on Bio-inspired Information and Communications Technologies (formerly BIONETICS)}, publisher={EAI}, proceedings_a={BICT}, year={2017}, month={3}, keywords={nanomechanical systems; nanomachines; nanomechanical communications; channel modeling; state transition}, doi={10.4108/eai.22-3-2017.152410} }
- Ahmed Nasif
Mohammad Upal Mahfuz
Jagadeep Thota
Year: 2017
A Framework of Nanomechanical Communication Systems Based on State Transitions
BICT
EAI
DOI: 10.4108/eai.22-3-2017.152410
Abstract
In this paper, the potential of nanomechanical (NM) components to serve as a nanomechanical communication (NMC) system is explored in detail. In particular, a framework to identify the key aspects relating to the mechanical dynamics of a NM system with information transfer between a pair of communicating nanomachines. The proposed model is generic in the sense that it captures the motion of the NM components comprising of a NM system, such as nanoscale actuators, sensors, hinges, valves, gears, springs, etc., without referring to their specific structures, compositions or operational mechanisms. Such components are modeled by categorizing their motions into four types: (i) linear-to-linear, (ii) linear-to-rotational, (iii) rotational-to-linear, and (iv) rotational-to-rotational. Current approach is to characterize the interface of any two nanomachines within a NM communication system. These two nanomachines can be adjacent (directly connected or coupled), or non-adjacent (indirectly connected or coupled) with other intervening NM components between them. These intervening NM components can also be nanomachines that work as relays in this case. The motion of a particular NM component is characterized by its motional degrees of freedom (MDOF), which is simply the number of discrete positions it can be in throughout its operation. Our model incorporates randomness due to thermal noise, ambient influences and other system uncertainties (like friction).