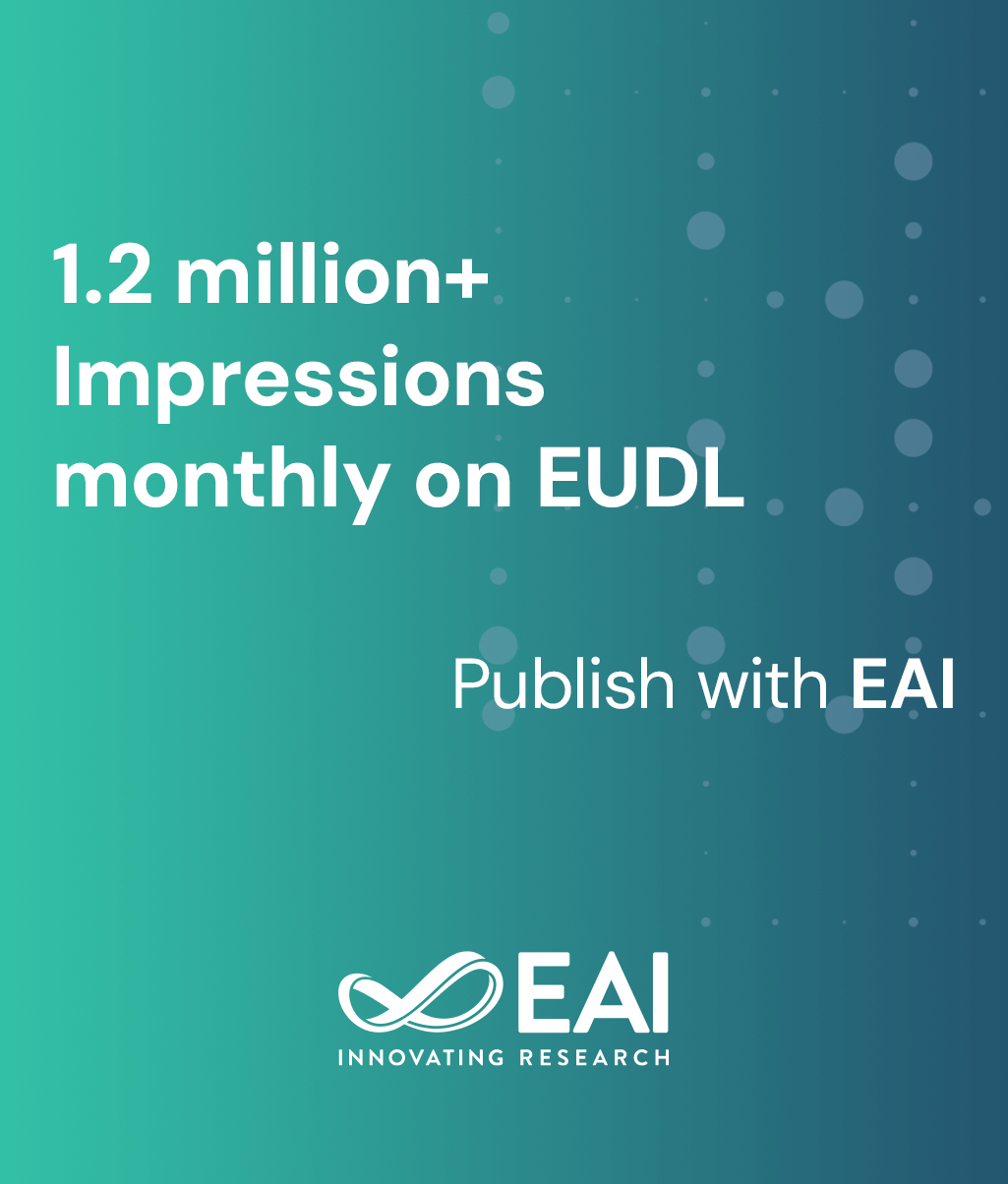
Research Article
Mechanical Properties of Geopolymer Grout with Bagasse Ash and Resin Catalyst
@INPROCEEDINGS{10.4108/eai.18-10-2019.2289999, author={Siti Isnaini Kurniawati Djaha and Hakas Prayuda and Fanny Monika and Martyana Dwi Cahyati and Fadillawaty Saleh}, title={Mechanical Properties of Geopolymer Grout with Bagasse Ash and Resin Catalyst}, proceedings={Proceedings of the 1st International Conference on Engineering, Science, and Commerce, ICESC 2019, 18-19 October 2019, Labuan Bajo, Nusa Tenggara Timur, Indonesia}, publisher={EAI}, proceedings_a={ICESC}, year={2019}, month={12}, keywords={grouting mechanical properties bagasse ash resin catalyst}, doi={10.4108/eai.18-10-2019.2289999} }
- Siti Isnaini Kurniawati Djaha
Hakas Prayuda
Fanny Monika
Martyana Dwi Cahyati
Fadillawaty Saleh
Year: 2019
Mechanical Properties of Geopolymer Grout with Bagasse Ash and Resin Catalyst
ICESC
EAI
DOI: 10.4108/eai.18-10-2019.2289999
Abstract
Concrete can crack which causes a decrease of performance in the structure of the building. It requires an improvement in the damage in the concrete so that the strength returns to normal. This research was conducted to find a mixture of materials with the appropriate composition in order to restore the strength of the damaged concrete by using a new mixture modification. The material used in this study is using bagasse ash derived from sugar mill waste and chemical resin catalyst as a substitute for water and binder. The mixture was made using 5 variations in the volume ratio of catalyst resin and bagasse ash, namely 1: 0.4, 1: 0.53, 1: 0.67, 1: 0.8, and 1: 1. This research tested the mechanical properties of the specimens that have been made from the mix proportion. The result of the research that has been shown is that the addition of sugarcane ash in a mixture with resin catalyst levels continues to increase in the compressive strength. The increasing age of the concrete also increases the value of compressive strength on the specimens. The highest compressive strength is obtained by mixing material with a ratio of 1: 1, it was 96.18 MPa. The grouting material that has been made is also less effective when injected into damaged parts of the concrete because it has a thick texture which makes the material difficult to inject so that it requires greater pressure than the grout material from a mixture of cement and water