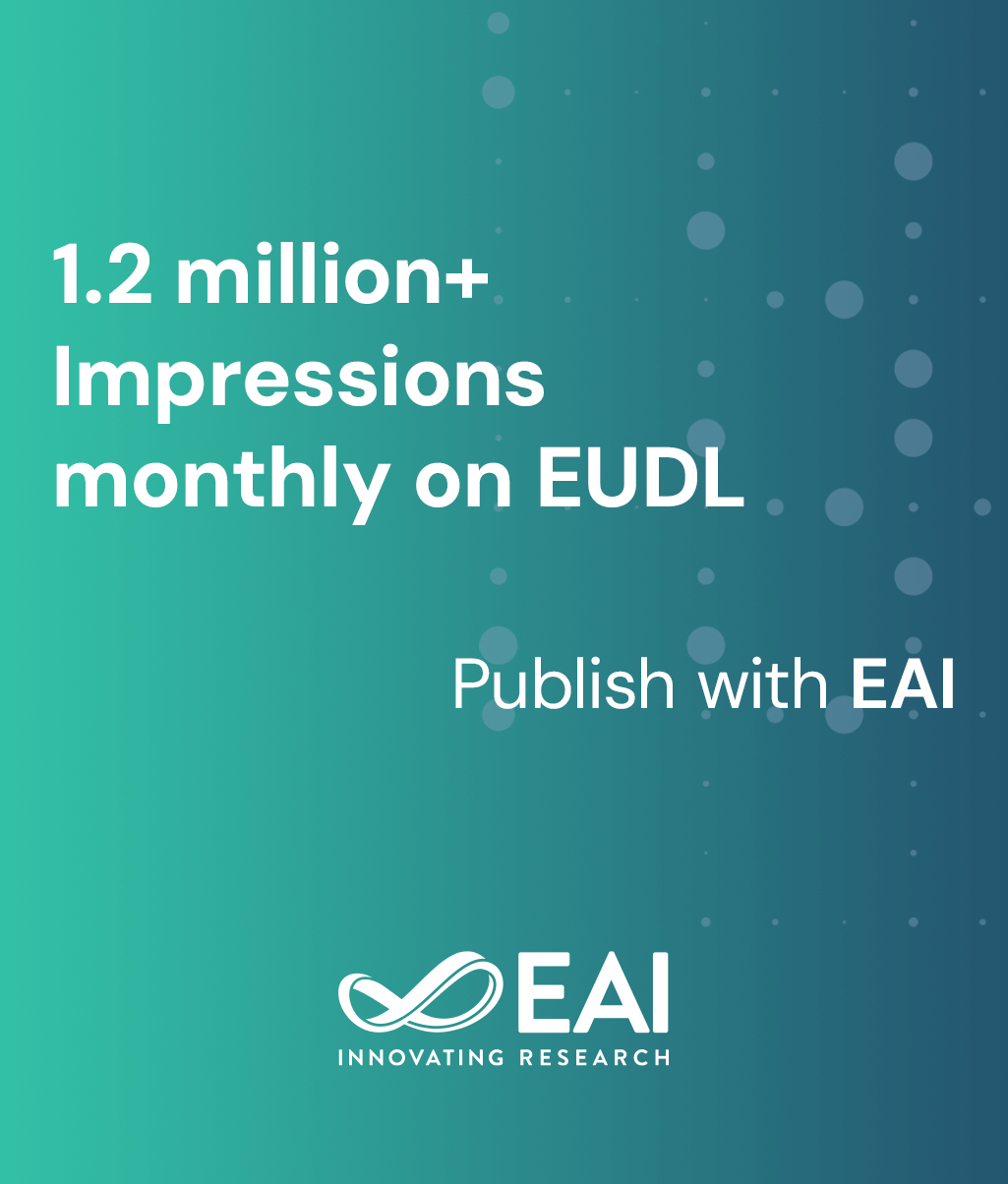
Research Article
Optimizing Robotic Arm Precision With Real-Time Machine Vision Feedback
@INPROCEEDINGS{10.4108/eai.17-11-2023.2342833, author={Anusuya K.V and Suberus Heartrisha G and Praveenbabu R S}, title={Optimizing Robotic Arm Precision With Real-Time Machine Vision Feedback}, proceedings={Proceedings of the First International Conference on Science, Engineering and Technology Practices for Sustainable Development, ICSETPSD 2023, 17th-18th November 2023, Coimbatore, Tamilnadu, India}, publisher={EAI}, proceedings_a={ICSETPSD}, year={2024}, month={1}, keywords={color segmentation contouring image segmentation inverse kinematics machine vision manipulator}, doi={10.4108/eai.17-11-2023.2342833} }
- Anusuya K.V
Suberus Heartrisha G
Praveenbabu R S
Year: 2024
Optimizing Robotic Arm Precision With Real-Time Machine Vision Feedback
ICSETPSD
EAI
DOI: 10.4108/eai.17-11-2023.2342833
Abstract
Industries play a vital role in the evolution of various innovations, and hardware and robotic arms are essential aids for automation. The main objective of a robotic arm is to perform infinite tasks in a variety of environments and can automate the execution of repetitive tasks. It is essential to update the design of robotic arms to achieve the desired accuracy. Most of the existing robotic arms use coordinate-based working space that results in offset errors in industrial applications where assembly lines are used. In this paper, machine vision is employed to cater to precision needs. On identification of the target site, the arm movements are generated accordingly. Further processing and movement of the arm synchronize, providing a solution to the offset-based problems. The arm moves to the desired target site with no error or misalignment based on the actions. The two major sections of the arms include Image Segmentation (IS) and Inverse Kinematics (IK) for machine vision and arm movement. These two parts are at the server end, and arm movement is attained through a separate microcontroller. However, the more extensive convergence time towards the desired target site is the limitation. Moreover, the prototype can be improved by using industry-standard tools and fine-tuning the design of processing parts. This prototype can be extended to various applications of high-level assembly line robotic manipulators in industries.