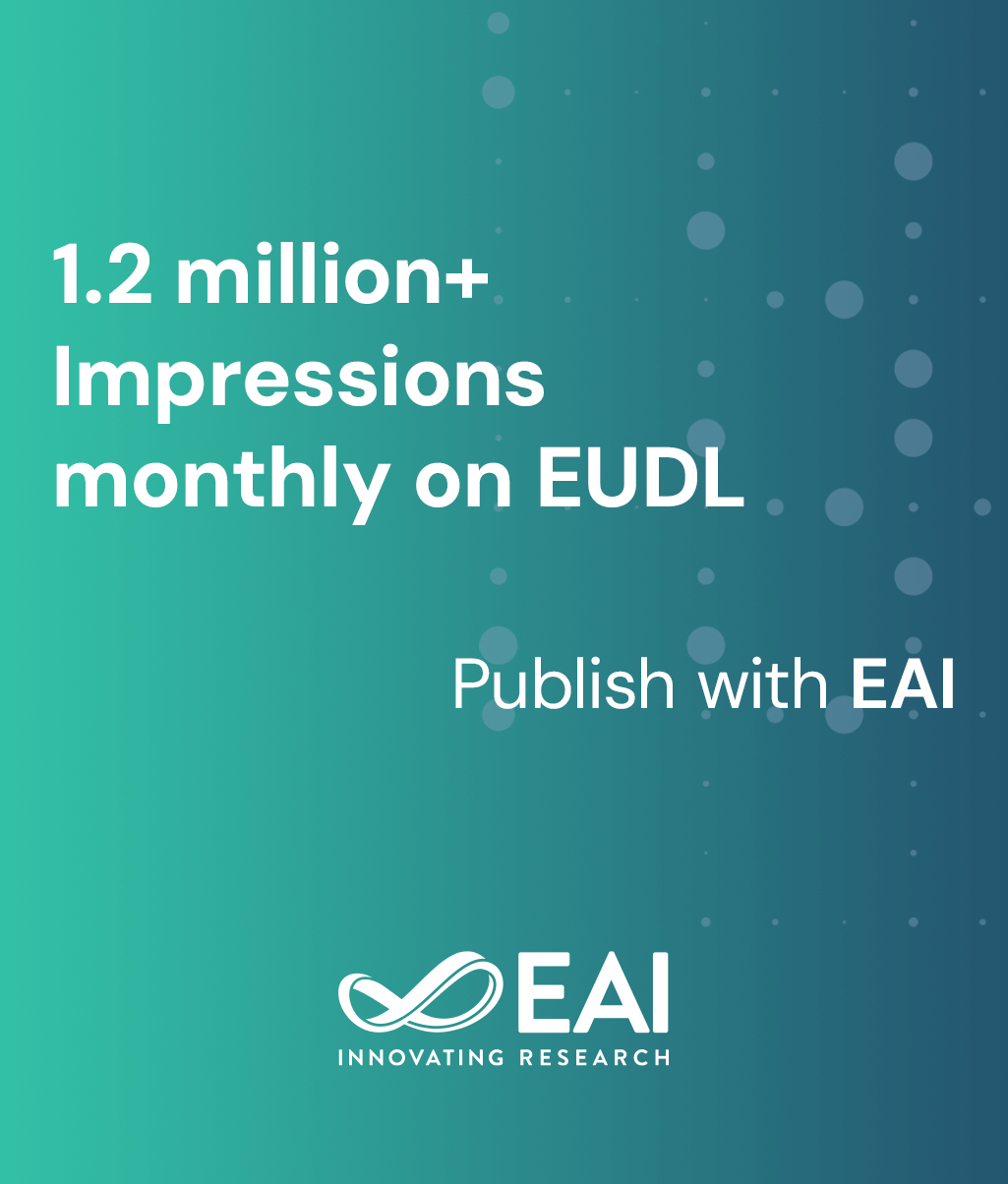
Research Article
The Effect of Adding ZrO2 Nanoparticles to Fe-18Al-15Cr Alloys with Mechanical Alloying Process for Oxidation Resistance
@INPROCEEDINGS{10.4108/eai.11-7-2019.2297717, author={Lolytah Lolytah and Djoko Hadi Prajitno and Pawawoi Pawawoi}, title={The Effect of Adding ZrO2 Nanoparticles to Fe-18Al-15Cr Alloys with Mechanical Alloying Process for Oxidation Resistance}, proceedings={Proceedings of the 1st International Conference on Islam, Science and Technology, ICONISTECH 2019, 11-12 July 2019, Bandung, Indonesia.}, publisher={EAI}, proceedings_a={ICONISTECH}, year={2021}, month={1}, keywords={fe3al intermetallic mechanical alloying oxidation zro2 nanoparticles }, doi={10.4108/eai.11-7-2019.2297717} }
- Lolytah Lolytah
Djoko Hadi Prajitno
Pawawoi Pawawoi
Year: 2021
The Effect of Adding ZrO2 Nanoparticles to Fe-18Al-15Cr Alloys with Mechanical Alloying Process for Oxidation Resistance
ICONISTECH
EAI
DOI: 10.4108/eai.11-7-2019.2297717
Abstract
The purpose of this study is to make a compatible material for the application at high temperatures. Material that commonly used is superalloy but this material has low melting point. One material that can replace superalloy material for the application at high temperatures are intermetallic alloys and this alloys are very compatible to facing up Industrial Revolution 4.0. The intermetallic alloys have several characteristics such as high strength at high temperatures, high oxidation resistance, high melting points and low densities. The specimens are made at this research are intermetallic alloys of Fe-18Al-15Cr with variations in the addition of ZrO2 nanoparticles (1%, 3% and 5%). The process of making specimens using one method of powder metallurgy. The process is Mechanical Alloying (MA) which aims to reduce the particle size, increase homogeneity and help to form new phases. In the high temperature oxidation process using a variable temperature at 800°C, 900°C and 1000°C for 4 hours. The result of metallographic testing showed the formation of the intermetallic phase Fe3Al. The result of XRD testing showed the formation of oxide compounds on the surface of the specimen that are Cr2O3, Al2O3 and Fe2O3. Addition of small amount of ZrO2 into the Fe-Al alloy is very effective to enhance the oxidation resistance and hardness of the material.