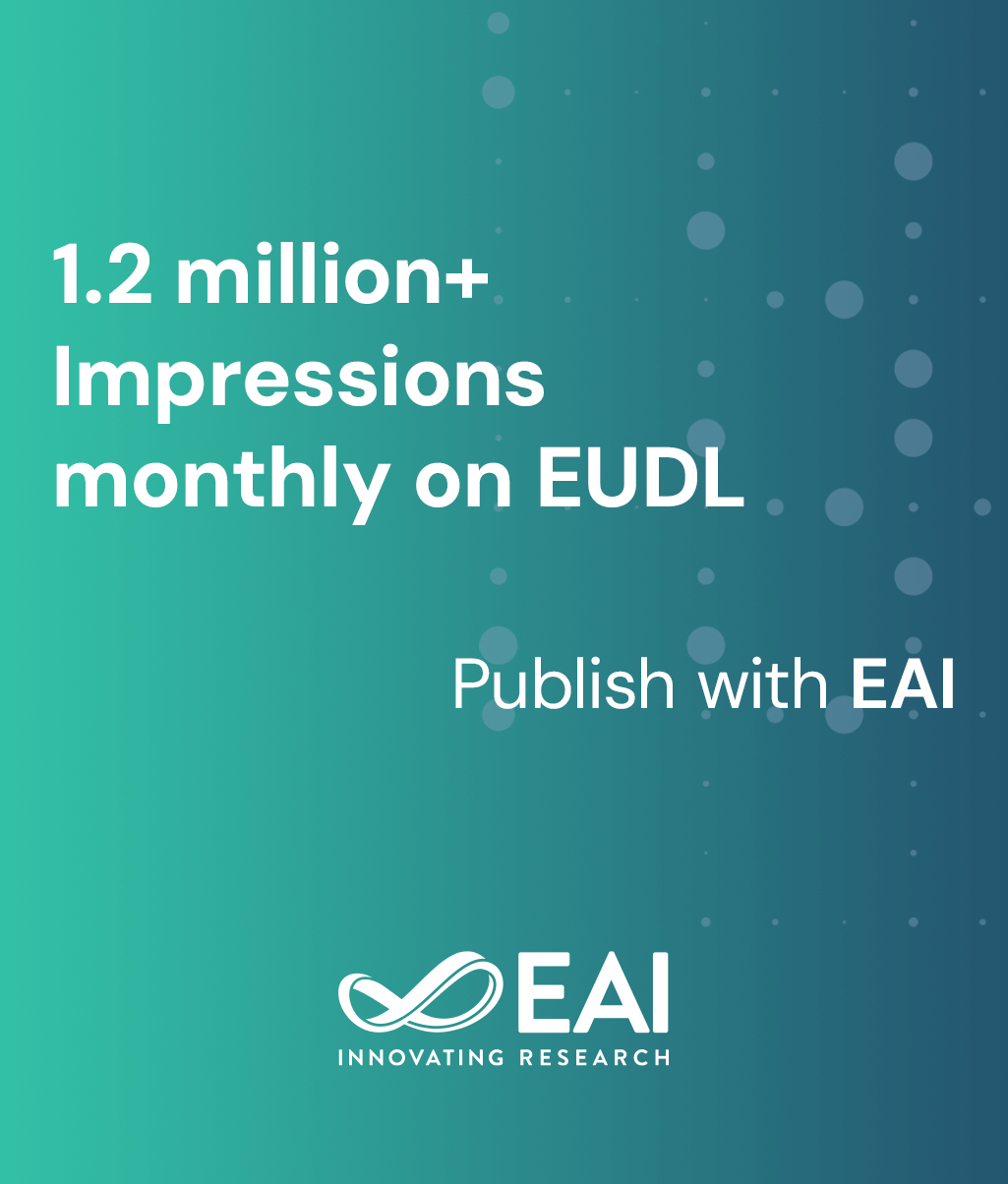
Research Article
Simulation and Control of the KUKA KR6 900EX Robot in Unity 3D: Advancing Industrial Automation through Virtual Environments
@ARTICLE{10.4108/airo.8026, author={Anand Ajayakumar Sujatha and Amin Kolahdooz and Mohammadreza Jafari and Alireza Hajfathalian}, title={Simulation and Control of the KUKA KR6 900EX Robot in Unity 3D: Advancing Industrial Automation through Virtual Environments}, journal={EAI Endorsed Transactions on AI and Robotics}, volume={4}, number={1}, publisher={EAI}, journal_a={AIRO}, year={2025}, month={3}, keywords={Unity 3D, Robotics Simulation, Creo, Automated Systems, Pick-and-Place Operations, Industrial Automation}, doi={10.4108/airo.8026} }
- Anand Ajayakumar Sujatha
Amin Kolahdooz
Mohammadreza Jafari
Alireza Hajfathalian
Year: 2025
Simulation and Control of the KUKA KR6 900EX Robot in Unity 3D: Advancing Industrial Automation through Virtual Environments
AIRO
EAI
DOI: 10.4108/airo.8026
Abstract
This study presents the development of a virtual simulation of a KUKA robot within the Unity 3D platform, focusing on its ability to execute pick-and-place operations in an industrial setting. The research emphasizes the importance of digital simulations as cost-effective and safe alternatives to physical prototypes in industrial automation. By replicating robotic tasks in a virtual environment, organizations can mitigate wear and tear on expensive machinery and minimize safety hazards inherent in real-world operations. The simulation process commenced with the creation of a detailed 3D model of the KUKA robot utilizing Creo CAD software. This model was subsequently imported into the Unity 3D environment, where an interactive and realistic simulation environment was constructed. A manual control system was implemented through custom C# scripts, enabling precise joint manipulation via keyboard inputs. While the current control mechanism remains manual, this study provides a foundational framework for the future integration of advanced algorithms for trajectory planning and autonomous control. The simulation successfully demonstrates the feasibility of performing industrial robotic tasks within a virtual environment. It serves as a platform for further research, including the automation of robotic movements and the integration of virtual reality and digital twin technologies. These advancements have the potential to significantly enhance real-time monitoring, operator training, and overall operational efficiency in industrial applications. This work underscores the growing significance of virtual simulation technologies in industrial automation, presenting a scalable and flexible solution for prototyping, testing, and training within complex industrial ecosystems.
Copyright © 2025 Anand Ajayakumar Sujatha et al., licensed to EAI. This is an open access article distributed under the terms of the CC BY-NC-SA 4.0, which permits copying, redistributing, remixing, transformation, and building upon the material in any medium so long as the original work is properly cited.