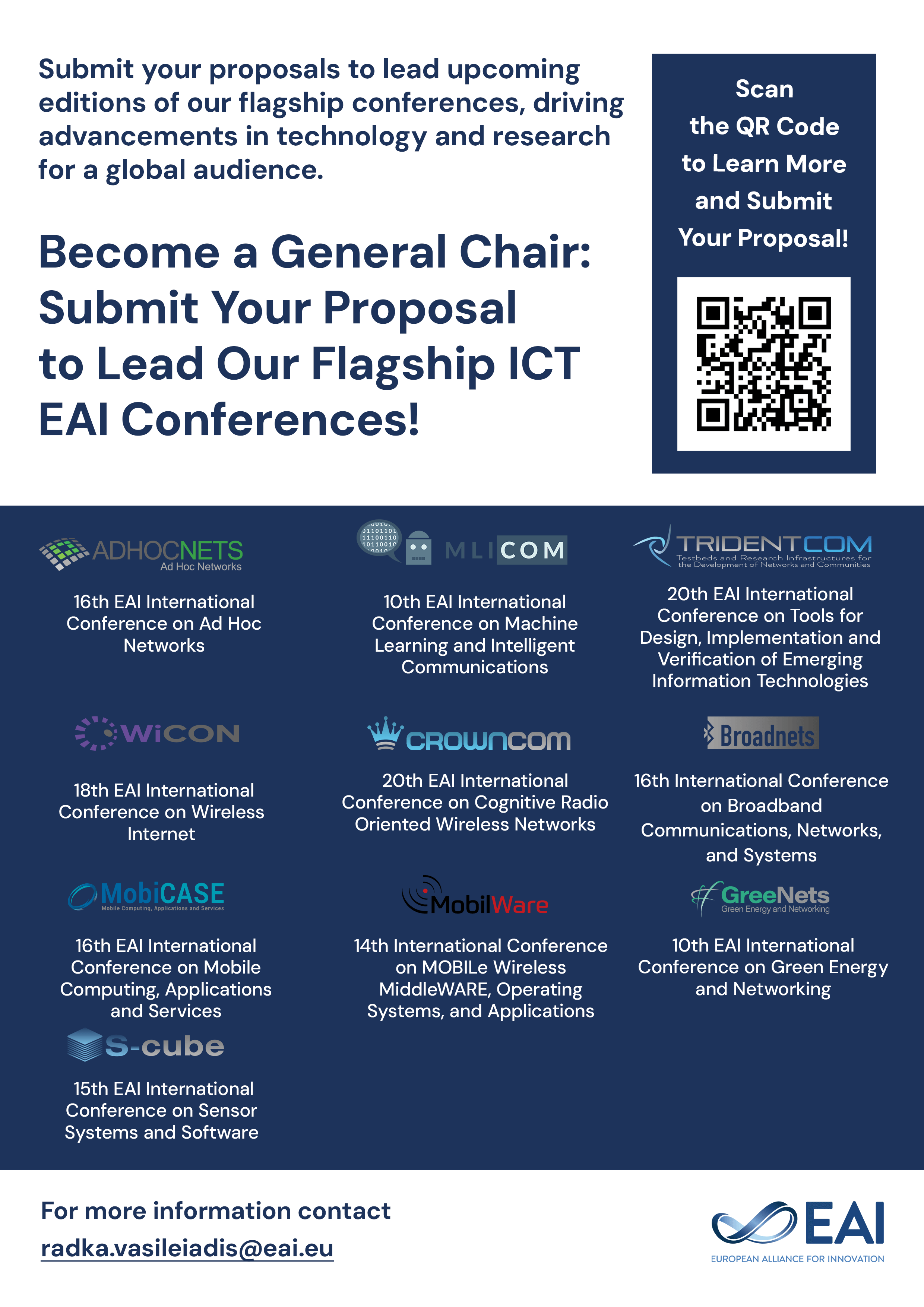
Research Article
Simulation of power-draw and fill level for a semi-autogenous mill system
@INPROCEEDINGS{10.4108/ICST.SIMUTOOLS2010.8707, author={Jos\^{e} Luis Salazar Navarrete and H\^{e}ctor Vald\^{e}s-Gonz\^{a}lez and Francisco Cubillos Montecino}, title={Simulation of power-draw and fill level for a semi-autogenous mill system}, proceedings={3rd International ICST Conference on Simulation Tools and Techniques}, publisher={ICST}, proceedings_a={SIMUTOOLS}, year={2010}, month={5}, keywords={Simulation; SAG milling; Comminution; Modeling.}, doi={10.4108/ICST.SIMUTOOLS2010.8707} }
- José Luis Salazar Navarrete
Héctor Valdés-González
Francisco Cubillos Montecino
Year: 2010
Simulation of power-draw and fill level for a semi-autogenous mill system
SIMUTOOLS
ICST
DOI: 10.4108/ICST.SIMUTOOLS2010.8707
Abstract
This poster present a dynamic simulator of a semi-autogenous grinding operation deduced from first principles coupled to an online parameter estimation scheme able to simulate industrial operations for future control purposes. The proposed procedure for simulation purposes is as follows: Model equations are based on a conventional non-stationary population balance approach to develop the necessary dynamic model of the semi-autogenous mill operation. The presented models are able to predict the timeevolution of key operating variables such as product flow rate, level charge, power-draw, load position and others, as functions of other important variables such as mill rotational speed and fresh feed characteristics. The set of ordinary differential equations was solved using MATLAB/SIMULINK as a graphic programming platform, a useful tool for understanding the grinding process. Additionally, this work presents results using dynamic simulations from a 1200 t/h copper–ore mill showing the effectiveness of the system to track the dynamic behaviour of the variables.