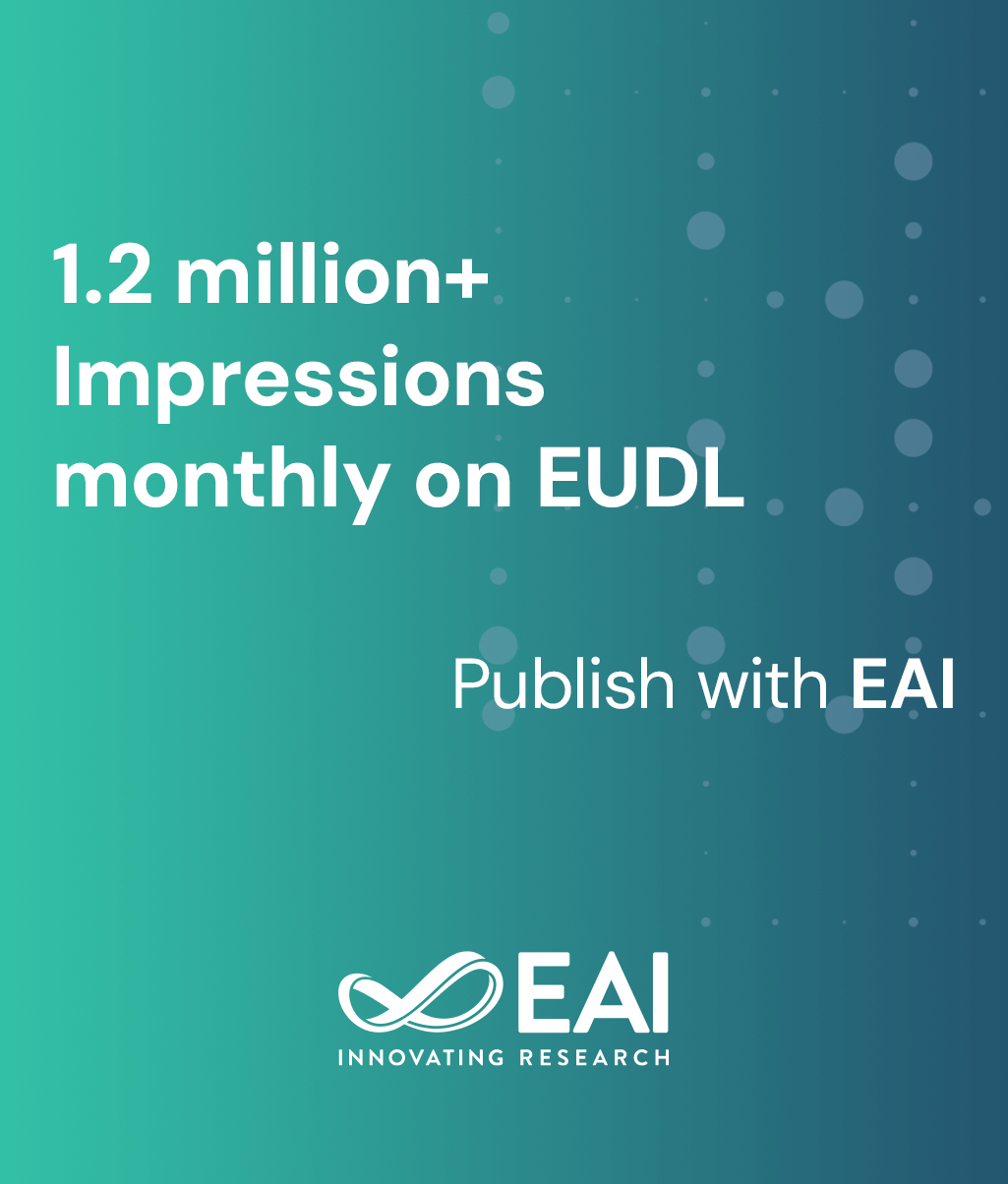
Research Article
Design and Testing of a Textile EMG Sensor for Prosthetic Control
@INPROCEEDINGS{10.1007/978-3-030-42029-1_3, author={Luisa Arruda and Alexandre Calado and Rachel Boldt and Yao Yu and Helder Carvalho and Miguel Carvalho and Fernando Ferreira and Filomena Soares and Dem\^{e}trio Matos}, title={Design and Testing of a Textile EMG Sensor for Prosthetic Control}, proceedings={IoT Technologies for HealthCare. 6th EAI International Conference, HealthyIoT 2019, Braga, Portugal, December 4--6, 2019, Proceedings}, proceedings_a={HEALTHYIOT}, year={2020}, month={6}, keywords={Textile electrode EMG Prostheses}, doi={10.1007/978-3-030-42029-1_3} }
- Luisa Arruda
Alexandre Calado
Rachel Boldt
Yao Yu
Helder Carvalho
Miguel Carvalho
Fernando Ferreira
Filomena Soares
Demétrio Matos
Year: 2020
Design and Testing of a Textile EMG Sensor for Prosthetic Control
HEALTHYIOT
Springer
DOI: 10.1007/978-3-030-42029-1_3
Abstract
Nowadays, Electromyography (EMG) signals generated by the amputee’s residual limbs are widely used for the control of myoelectric prostheses, usually with the aid of pattern-recognition algorithms. Since myoelectric prostheses are wearable medical devices, the sensors that integrate them should be appropriate for the users’ daily life, meeting the requirements of lightness, flexibility, greater motion identification, and skin adaptability. Therefore, this study aims to design and test an EMG sensor for prosthetic control, focusing on aspects such as adjustability, lightness, precise and constant signal acquisition; and replacing the conventional components of an EMG sensor with textile materials. The proposed sensor was made with - + B conductive knitted fabric, with 99% pure silver plating. EMG data acquisition was performed twice on three volunteers: one with the textile sensor, and other with a commercial sensor used in prosthetic applications. Overall, the textile and the commercial sensor presented total average Signal-to-Noise Ratio (SNR) values of 10.24 ± 5.45 dB and 11.74 ± 8.64 dB, respectively. The authors consider that the obtained results are promising and leave room for further improvements in future work, such as designing strategies to deal with known sources of noise contamination and to increase the adhesion to the skin. In sum, the results presented in this paper indicate that, with the appropriate improvements, the proposed textile sensor may have the potential of being used for myoelectric prosthetic control, which can be a more ergonomic and accessible alternative to the sensors that are currently used for controlling these devices.